PCB特殊工藝分享
- 發(fā)布時間:2024-09-19 17:21:32
- 瀏覽量:855
1、金手指Tie bar less工藝(Removal Of Gold Finger Plating Tie Bar)
隨著PCIe Gen5接口的出現(xiàn),各種PCB工藝也需要同步以滿足PCIe Gen5的工藝要求。因此,Tie bar less工藝就成為PCB廠家必修的工藝之一。下圖顯示了英特爾最新的PCIe Gen5布局指南;
金手指通過鍍金線電鍍硬金,再通過PCB工藝蝕刻掉鍍金線(保留部分覆上干膜),減少高速信號的信號損耗從而實現(xiàn)更好的信號傳輸:
蝕刻鍍金線時一般有兩種Tie bar less工藝,用于減少Tie bar的產(chǎn)生:
從可靠性的角度來看,一般選擇無undercut設(shè)計會更好,以避免插拔后金面undercut處翹起或塌陷
2、 板邊電鍍(Edge Plating)
PCB的鍍邊是指從電路板TOP延伸到BOT并沿電路板一側(cè)邊緣的鍍層。在制造過程中,需要金屬化的邊緣在鍍銅/金前進(jìn)行數(shù)控銑削,鍍銅/金后對PCB的邊緣進(jìn)行適當(dāng)?shù)谋砻嫣幚?
鍍邊在PCB上的設(shè)計應(yīng)用:
1)增強電流傳導(dǎo)
2)信號的完整性
鍍邊通過防止干擾進(jìn)入信號內(nèi)部傳輸,提高了PCB的信號完整性
3)熱分布
由于邊緣鍍層的金屬性質(zhì),其提供了額外的冷卻表面積以將熱量散發(fā)到周圍的空氣中,并提高了PCB的可靠性(特別是對于熱敏性的元件)
4)提高EMC/EMI性能
邊緣鍍層允許雜散電流的逃逸,防止產(chǎn)生零星的電場和磁場,這有助于保持更好的EMC/EMI性能
5)防止靜電損壞
在處理PCB時,靜電可能會放電到敏感元件上。金屬表面有助于吸收靜電,防止靜電損壞。
3、特殊工藝專用名詞統(tǒng)計
POFV (plate over filled via) 盤中孔
PIP(Pin in Paste)回流焊工藝焊接通孔元器件==PIH (Paste-In-Hole) 通孔印錫膏
Press Fit 無焊錫組裝工藝:壓接
PTH(Plated Through Hole)鍍通孔
HASL(Hot Air Solder Leveling)熱風(fēng)焊錫整平
OSP(Organic Solderability Preservative)有機可焊性保護(hù)層
ENIG(Electroless nickel immersion gold)沉鎳金
ImSn(immersion Stannum)沉錫
ImAg(immersion Argentum)沉銀
ENEPIG(Electroless Nickel Electroless Palladium Immersion Gold)沉鎳鈀金
Gold Plating 電金,鍍金
AOI (Automatic Optical Inspection) 自動光學(xué)檢測
ICT(In-Circuit-Test)在線測試
PP(Panel Plating) 板電
Deburring 去毛刺(沉銅前磨板
backdrill 背鉆
Bare Copper 裸銅
BVH(Blind Via Hole)盲孔
4、工藝流程專業(yè)名詞
•Sheets Cutting
Cut the substrate to the working panel according to the material dimension on the work order.
•Scrub
Before lamination, the copper foil on the board should be roughened by brushing, micro-etching, etc., and then the dry film photoresist should be tightly attached to it with appropriate temperature and pressure.
•Dry Film Lamination
The board is proceed with pre-treatment to clean and micro-etch , the surface of the board is cleaned and micro-etched, and then sent to the lamination machine for lamination, and a photosensitive organic film is covered on the surface of the board. After exposure, the circuit pattern of the negative film is transferred to the board.
•Exposure
The board with the dry film is sent to the exposure machine for exposure. The dry film will be photosensitive after being irradiated by UV light in the light-transmitting area of the negative film, and the circuit image on the negative film will be transferred to the board surface.
•Inner Developing
During the development phase in PCB flow, the alkaline solution is used to wash out left unhardened photoresists. After that, the inner layer image is printed by blue resist, which will resist the chemical solution at the etching stage.
•Inner Etching
The etching is a key stage of layer imaging, using an acid solution to remove unwanted copper and outline the pattern. After etching, the board is cleaned to wash out the excess chemical solution.
•Inner Stripping
Stripping is to completely peel off the exposed dry photoresist film that protects the copper surface with sodium hydroxide solution to expose the circuit pattern.
•Black Oxide Treatment
The purpose of the brown oxide treatment is to form a microscopic roughness and organic metal layer on the inner layer surface through a chemical treatment to enhance the adhesion between the layers and avoid such problems as delamination.
•Lamination
In actual operation, the discrete multi-layer board and prepreg are pressed together to form a multi-layer board with the required number of layers and thickness. Finally, the copper foil completes the stack-up in pcb process flow The combinations of a copper foil and a prepreg are located on the top and bottom respectively, sandwiching the inner layer to form the stack-up.
The stack-up is processed in the lamination machine, which takes up to 2 hours. After processing under high pressure and temperature, a single laminated board is formed and then moved to the cold press. In this stage, various factors such as the uniformity of copper distribution, the symmetry of the stack, the design and layout of the blind and buried holes must be considered in detail during the design.
•Drilling
Drilling has 2 main purposes, one is to connect load components, another is to link the copper layers. In this stage, there is no copper in the holes, therefore the current cannot flow through the board.
•Desmear
In desmear process friction-melted resin and drilling debris are removed from drill holes. This is achieved by permanganate or plasma treatment. Certain processes can also improve coating adhesion of the resin by micro roughening.
•Copper Plating
The drilled PCB board undergoes an oxidation-reduction reaction in the sinking copper cylinder to form a copper layer to metalize the holes. The copper is deposited on the surface of the originally insulated substrate to obtain conductive holes, thereby achieving electrical communication between the inner layer and outer layer. The stage of printed circuit board production process takes place in a series of chemical and rinsing baths.
•Outer Layer Etching
There are three main steps in PCB flow. Firstly, all residues and the dry film are removed, but the unwanted copper remains. Next, the board passes through the chemical solution to etch away the unwanted copper and tin. Finally, the circuit areas and connections are properly defined.
•Solder Mask
Solder mask is one of the most critical stages in the production of printed circuit boards, mainly by screen printing or coating solder mask ink to coat a layer of solder mask on the surface of the board. Through exposure and development, the pads and holes are exposed, and the solder mask is hardened. Finally, the unprotected and unhardened portions by insolation will be washed out.
•Surface Finish
The solderability of bare copper itself is pretty good, but long-term exposure to the air is easy to be damp and oxidized. The bare copper tends to exist in the form of oxide, which is unlikely to remain in its original state for a long time. Therefore, surface treatment of the copper surface is required to ensure good solderability and electrical properties. The most common surface treatments are immersion tin, electroless nickel immersion gold (ENIG), immersion silver, gold plating, etc.
•Silkscreen
This stage prints the required characters or part symbols on the board surface by screen printing, and then exposes it under the UV light.
•CNC-Routing
Cut the PCB to the required shape and dimensions.
•Electrical Test
Simulate the state of the PCB board and check the electrical performance to see if there is an open or short circuit.
•O.Q.C.
Check the appearance, size, hole diameter, thickness, marking, etc. of the board to meet customer requirements. The qualified products are packed into bundles, which are easy to store and transport.
————————————————
版權(quán)聲明:本文為博主原創(chuàng)文章,遵循 CC 4.0 BY-SA 版權(quán)協(xié)議,轉(zhuǎn)載請附上原文出處鏈接和本聲明。
blog.csdn.net/qq_41904778/article/details/135126376
免責(zé)聲明:部分文章信息來源于網(wǎng)絡(luò)以及網(wǎng)友投稿,本網(wǎng)站只負(fù)責(zé)對文章進(jìn)行整理、排版、編輯,意為分享交流傳遞信息,并不意味著贊同其觀點或證實其內(nèi)容的真實性,如本站文章和轉(zhuǎn)稿涉及版權(quán)等問題,請作者在及時聯(lián)系本站,我們會盡快和您對接處理。
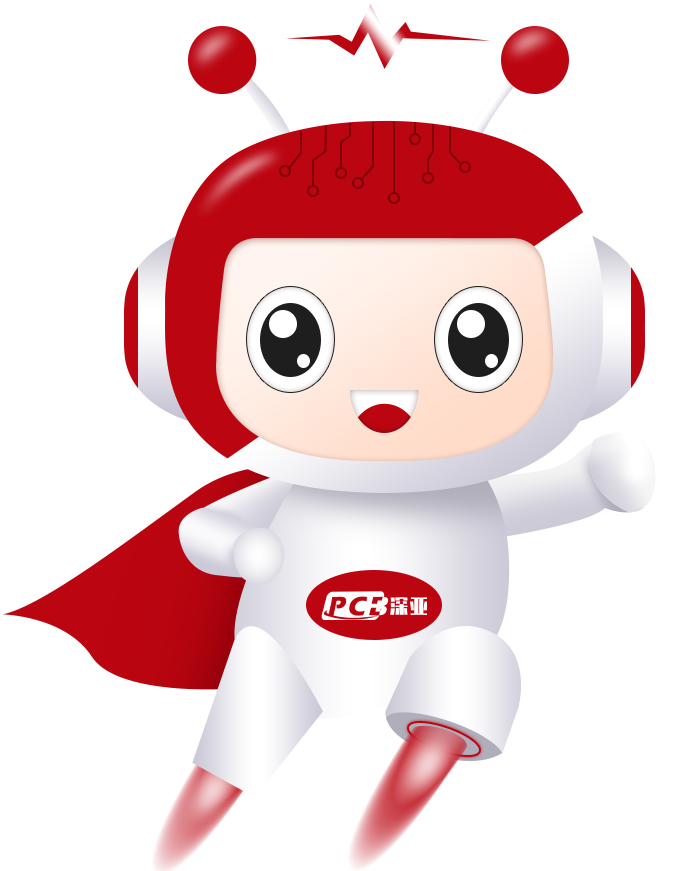